Introduction: Navigating the Global Market for 3d printed dental implants
As the dental industry continues to evolve, 3D printed dental implants are emerging as a transformative solution, offering precision, efficiency, and customization that traditional methods struggle to match. For B2B buyers across Africa, South America, the Middle East, and Europe, understanding this technological advancement is crucial for informed sourcing decisions. The global market for 3D printed dental implants is not just about the products themselves; it encompasses a wide range of factors including types of implants, materials used, manufacturing processes, quality control measures, and supplier networks.
This comprehensive guide serves as a valuable resource for international buyers seeking to navigate the complexities of this dynamic market. We will delve into the various types of 3D printed dental implants, exploring their unique benefits and applications. Additionally, we will examine the materials that ensure biocompatibility and durability, alongside the manufacturing and quality assurance processes that guarantee high standards.
Understanding the cost implications, market trends, and key players in the industry will also be a focal point of this guide. By addressing frequently asked questions, we aim to empower decision-makers with the insights needed to make strategic purchases that align with their operational needs and customer expectations. Whether you are based in Johannesburg, Buenos Aires, Dubai, or Berlin, this guide will equip you with the knowledge to enhance your procurement strategies and capitalize on the opportunities presented by 3D printing technology in dental applications.
Understanding 3d printed dental implants Types and Variations
Type Name | Key Distinguishing Features | Primary B2B Applications | Brief Pros & Cons for Buyers |
---|---|---|---|
Titanium Implants | High strength, biocompatibility, and corrosion resistance | Long-term dental restorations | Pros: Durable, widely accepted; Cons: Higher cost compared to other materials. |
Zirconia Implants | Aesthetic appeal, metal-free, and excellent biocompatibility | Cosmetic dentistry and aesthetic cases | Pros: Natural appearance; Cons: Less strength than titanium. |
Resin-based Implants | Lightweight, customizable, and cost-effective | Temporary solutions and dental trials | Pros: Lower cost, easy to print; Cons: Shorter lifespan and durability. |
Custom Implants | Tailored design for specific patient needs | Complex cases requiring unique shapes | Pros: Enhanced fit and function; Cons: Longer production time and higher costs. |
Hybrid Implants | Combination of materials (e.g., titanium and ceramic) | Versatile applications in various cases | Pros: Balances strength and aesthetics; Cons: Complexity in manufacturing. |
Titanium Implants
Titanium implants are a staple in dental restoration due to their strength and biocompatibility. These implants are often used in long-term dental solutions, such as replacing missing teeth or anchoring bridges. For B2B buyers, the key considerations include the initial investment, as titanium implants tend to be more expensive, but their durability can lead to lower long-term costs.
Zirconia Implants
Zirconia implants are increasingly popular for their aesthetic advantages, providing a natural look that appeals to patients concerned about the visibility of metal. They are commonly utilized in cosmetic dentistry, especially for anterior teeth. Buyers should weigh the benefits of aesthetics against the potential for reduced strength compared to titanium, making them less suitable for high-stress areas.
Resin-based Implants
Resin-based implants are lightweight and customizable, making them a cost-effective option for temporary solutions or dental trials. They are ideal for use in situations where a quick turnaround is necessary, such as in dental schools or for immediate restorations. However, buyers must consider the trade-off in longevity, as these implants typically have a shorter lifespan compared to metal options.
Custom Implants
Custom implants are designed to meet the specific anatomical needs of patients, making them particularly useful in complex cases where standard implants may not suffice. The tailored approach enhances the fit and function of the implant, providing better outcomes for patients. B2B buyers should be prepared for potentially higher costs and longer production times, as custom designs require more intricate planning and manufacturing.
Hybrid Implants
Hybrid implants combine materials like titanium and ceramic to leverage the strengths of both. This versatility allows them to be used in various applications, from aesthetic enhancements to functional restorations. Buyers should consider the complexity of manufacturing these implants, which may result in higher costs and require careful supplier selection to ensure quality and reliability.
Related Video: Formlabs Dental: 3D Printed Digital Dentures
Key Industrial Applications of 3d printed dental implants
Industry/Sector | Specific Application of 3D Printed Dental Implants | Value/Benefit for the Business | Key Sourcing Considerations for this Application |
---|---|---|---|
Dental Clinics | Customized dental implants for individual patients | Enhanced patient satisfaction and faster recovery times | Ensure suppliers offer biocompatible materials and customization options. |
Dental Laboratories | Production of dental prosthetics and crowns | Reduced lead times and lower production costs | Look for reliable 3D printers with high precision and material versatility. |
Orthodontics | Creation of orthodontic devices | Improved treatment outcomes and patient comfort | Source implants that allow for easy adjustments and have proven durability. |
Maxillofacial Surgery | Reconstruction implants for facial injuries | High-quality, tailored solutions that meet specific needs | Consider suppliers with experience in complex implant designs and bioengineering. |
Veterinary Dentistry | Specialized implants for animal dental care | Expansion of service offerings and enhanced animal welfare | Seek materials that are safe for animal use and have relevant certifications. |
Detailed Applications of 3D Printed Dental Implants
Dental Clinics: 3D printed dental implants enable clinics to provide customized solutions tailored to individual patient needs. This technology allows for the creation of implants that fit precisely, which can significantly enhance patient satisfaction and speed up recovery times. For international buyers, particularly in regions like Africa and South America, sourcing from suppliers who can offer biocompatible materials and customization options is crucial to meet diverse patient requirements.
Dental Laboratories: In dental laboratories, 3D printing technology streamlines the production of dental prosthetics and crowns. By utilizing 3D printed dental implants, labs can reduce lead times and lower production costs, making them more competitive. Buyers should prioritize suppliers that offer reliable 3D printers capable of high precision and material versatility, ensuring they can meet varying demands from dental practices.
Orthodontics: The orthodontics sector benefits from 3D printed dental implants by creating devices that improve treatment outcomes and patient comfort. These implants can be customized for each patient, enhancing the effectiveness of orthodontic treatments. B2B buyers should seek implants that allow for easy adjustments and have a proven track record of durability, particularly in markets like the Middle East and Europe where patient expectations are high.
Maxillofacial Surgery: In maxillofacial surgery, 3D printed implants play a critical role in reconstructive procedures for facial injuries. The ability to create high-quality, tailored solutions that meet specific anatomical needs is invaluable in this field. Buyers should consider suppliers with expertise in complex implant designs and bioengineering, as this ensures the implants not only fit well but also integrate effectively with the surrounding tissues.
Veterinary Dentistry: The veterinary sector is increasingly adopting 3D printed dental implants for animal dental care. This innovation expands service offerings and enhances animal welfare by providing specialized solutions for dental issues in pets. When sourcing materials for veterinary use, it is essential to select those that are safe and have relevant certifications to ensure compliance with health standards, particularly in regions with stringent regulations.
Related Video: Project ‘Poo Zoo’ uses animal dung to save at-risk species | REUTERS
Strategic Material Selection Guide for 3d printed dental implants
When selecting materials for 3D printed dental implants, international B2B buyers must consider various factors that influence performance, cost, and regulatory compliance. Below, we analyze four common materials used in the production of 3D printed dental implants, focusing on their properties, advantages, disadvantages, and specific considerations for buyers from Africa, South America, the Middle East, and Europe.
Titanium Alloys
Key Properties:
Titanium alloys, particularly Ti-6Al-4V, are renowned for their excellent strength-to-weight ratio and biocompatibility. They exhibit high corrosion resistance and can withstand significant mechanical loads, making them ideal for dental implants.
Pros & Cons:
The durability of titanium alloys is a significant advantage, as they can endure the stresses of chewing and grinding. However, the manufacturing process can be complex and costly, which may increase the final price of the implants. While they are suitable for long-term applications, their higher cost may deter some buyers.
Impact on Application:
Titanium alloys are compatible with various biological media, ensuring minimal adverse reactions in the human body. Their mechanical properties make them suitable for load-bearing applications.
Considerations for International Buyers:
Buyers must ensure compliance with international standards such as ASTM F136. Additionally, understanding local regulations regarding titanium sourcing and processing is crucial, especially in regions with stringent import laws.
Zirconia
Key Properties:
Zirconia (ZrO2) is a ceramic material known for its high strength, fracture toughness, and aesthetic appeal. It is also highly resistant to wear and corrosion, making it a suitable choice for dental applications.
Pros & Cons:
One of the key advantages of zirconia is its excellent aesthetic properties, which closely mimic natural teeth. However, it is generally less durable than titanium under high-stress conditions, which may limit its use in certain applications. The manufacturing process can be less complex compared to metals, potentially lowering costs.
Impact on Application:
Zirconia is particularly suitable for anterior dental implants where aesthetics are paramount. Its biocompatibility ensures that it is safe for long-term use in the body.
Considerations for International Buyers:
Buyers should look for compliance with standards such as ISO 6872 and be aware of the varying acceptance of zirconia in different regions, especially in markets where metal implants are preferred.
PEEK (Polyether Ether Ketone)
Key Properties:
PEEK is a high-performance polymer known for its excellent mechanical properties and biocompatibility. It has a high temperature resistance and is chemically inert, making it suitable for various dental applications.
Pros & Cons:
The lightweight nature of PEEK makes it comfortable for patients, and its resistance to wear and deformation under stress is advantageous. However, it may not be as strong as titanium for load-bearing applications, and its cost can be relatively high compared to other polymers.
Impact on Application:
PEEK is particularly useful in cases where flexibility and comfort are prioritized, such as in temporary implants or in conjunction with other materials.
Considerations for International Buyers:
Compliance with ASTM F2026 is essential. Buyers should also consider the availability of PEEK and its acceptance in specific markets, especially where traditional materials dominate.
Dental Resins
Key Properties:
Dental resins are versatile materials used for temporary and permanent dental restorations. They offer good aesthetics and can be formulated for various mechanical properties.
Pros & Cons:
The primary advantage of dental resins is their ability to be customized for specific applications, offering a balance between cost and performance. However, they may not provide the same level of durability as metals or ceramics, limiting their use in high-stress situations.
Impact on Application:
Dental resins are ideal for temporary implants and prosthetics, where aesthetics and ease of fabrication are critical.
Considerations for International Buyers:
Buyers should ensure that the resins meet local regulatory standards, such as ISO 10993 for biocompatibility, and consider the availability of specific formulations in their region.
Summary Table
Material | Typical Use Case for 3D Printed Dental Implants | Key Advantage | Key Disadvantage/Limitation | Relative Cost (Low/Med/High) |
---|---|---|---|---|
Titanium Alloys | Permanent implants | Excellent strength-to-weight ratio | High manufacturing complexity and cost | High |
Zirconia | Anterior implants | Aesthetic appeal | Less durable under high stress | Medium |
PEEK | Temporary implants | Lightweight and comfortable | Lower strength compared to metals | High |
Dental Resins | Temporary and aesthetic restorations | Customizable for specific applications | Limited durability under stress | Low |
This strategic material selection guide provides B2B buyers with essential insights into the various materials available for 3D printed dental implants, helping them make informed decisions that align with their operational needs and market demands.
In-depth Look: Manufacturing Processes and Quality Assurance for 3d printed dental implants
Manufacturing Processes for 3D Printed Dental Implants
The production of 3D printed dental implants involves a series of carefully controlled manufacturing stages. Each stage is crucial for ensuring the final product meets the stringent requirements of dental applications. Below, we delve into the main stages of manufacturing, key techniques employed, and how these processes can impact international B2B buyers.
1. Material Preparation
The choice of materials is fundamental in the manufacturing of dental implants. Common materials include titanium, zirconia, and biocompatible polymers.
- Material Selection: Titanium is favored for its strength and biocompatibility, while zirconia is known for its aesthetic properties. Polymers are increasingly used for temporary implants.
- Pre-processing: Materials often undergo pre-processing treatments such as cleaning, drying, and sometimes, pre-mixing with additives to enhance specific properties.
- Quality Control: Before moving to the next stage, materials are subjected to quality checks to ensure they meet specifications regarding purity and particle size.
2. Forming
This stage involves the actual 3D printing process, where the prepared materials are transformed into the desired implant shape.
- 3D Printing Techniques:
- Selective Laser Sintering (SLS): Utilizes a laser to fuse powdered materials, ideal for metal implants.
- Stereolithography (SLA): Employs UV light to cure liquid resin, suitable for high-precision models.
-
Binder Jetting: Involves the application of a binding agent to the powder, allowing for complex geometries.
-
Layering Process: The implant is built layer by layer, which allows for intricate designs but requires precision in alignment and adhesion.
3. Assembly
Post-printing, the implants may require assembly or integration with other components, depending on the design specifications.
- Component Integration: Some implants may consist of multiple parts that need to be assembled. This requires careful handling to avoid contamination or damage.
- Post-processing: This may involve additional treatments such as sintering or annealing to enhance the mechanical properties of the implant.
4. Finishing
Finishing processes are critical for achieving the desired surface characteristics and ensuring the implant’s compatibility with human tissues.
- Surface Treatment: Techniques such as sandblasting, polishing, or coating with bioactive materials enhance osseointegration.
- Final Quality Check: Before the implants are packaged, they undergo a final inspection to verify dimensional accuracy and surface finish.
Quality Assurance Standards and Procedures
Quality assurance is paramount in the manufacturing of dental implants, especially given the potential risks associated with implants. Compliance with international and industry-specific standards is essential.
International Standards
- ISO 9001: This standard ensures that organizations meet customer and regulatory requirements consistently. It focuses on quality management systems and continuous improvement.
- ISO 13485: Specifically for medical devices, this standard outlines requirements for a quality management system that demonstrates the ability to provide medical devices and related services that consistently meet customer and regulatory requirements.
Industry-Specific Certifications
- CE Marking: Essential for products sold in the European Economic Area, CE marking demonstrates compliance with health, safety, and environmental protection standards.
- FDA Approval: In the United States, implants must be approved by the Food and Drug Administration, ensuring they are safe and effective.
Quality Control Checkpoints
Quality control (QC) checkpoints are integral to ensuring the reliability and safety of 3D printed dental implants. Common QC checkpoints include:
- Incoming Quality Control (IQC): Initial inspections of raw materials to confirm they meet specified standards.
- In-Process Quality Control (IPQC): Monitoring during the manufacturing process to ensure adherence to parameters, allowing for immediate corrections.
- Final Quality Control (FQC): Comprehensive testing of the finished product, including dimensional checks and biocompatibility assessments.
Common Testing Methods
Various testing methods are employed to ensure the quality and safety of dental implants:
- Mechanical Testing: Evaluates the strength and durability of the implants through tensile, compression, and fatigue tests.
- Biocompatibility Testing: Assesses how the materials interact with biological systems, often using ISO 10993 standards as a guideline.
- Sterilization Validation: Ensures that the sterilization processes (e.g., autoclaving, gamma irradiation) are effective and do not compromise the implant’s integrity.
Verifying Supplier Quality Control
For international B2B buyers, particularly those in Africa, South America, the Middle East, and Europe, it’s crucial to verify the quality control processes of suppliers. Here are actionable steps:
- Supplier Audits: Conduct regular audits of suppliers to assess their compliance with quality standards. Look for certifications and evidence of consistent quality practices.
- Request Documentation: Ask for quality assurance reports, including IQC, IPQC, and FQC documentation, to understand their testing and inspection processes.
- Third-Party Inspections: Engage independent third-party inspectors to validate the supplier’s quality claims and ensure impartiality.
Conclusion
Understanding the manufacturing processes and quality assurance measures for 3D printed dental implants is essential for B2B buyers aiming to ensure the safety, efficacy, and compliance of the products they procure. By focusing on material preparation, forming, assembly, and finishing stages, along with rigorous quality control practices, buyers can make informed decisions that enhance the overall quality of their dental offerings. Always prioritize suppliers who adhere to international standards and provide transparent quality assurance documentation to mitigate risks associated with dental implants.
Related Video: How to Perform Dental Implants by MIS -Tutorial (3D Dental Animation)
Comprehensive Cost and Pricing Analysis for 3d printed dental implants Sourcing
When sourcing 3D printed dental implants, understanding the cost structure and pricing components is essential for international B2B buyers. The costs involved can be categorized into several key components, each influencing the final price of dental implants.
Cost Components
-
Materials: The choice of materials significantly impacts the overall cost. High-quality biocompatible materials, such as titanium or zirconia, tend to be more expensive but offer enhanced performance and durability. Buyers should consider the specific requirements of their market when selecting materials to balance quality and cost.
-
Labor: Labor costs include the wages for skilled technicians who operate 3D printers and conduct post-processing tasks. In regions like Africa and South America, labor costs may be lower than in Europe or the Middle East, potentially offering a cost advantage. However, ensure that the workforce is adequately trained to maintain quality standards.
-
Manufacturing Overhead: This encompasses costs related to utilities, maintenance of equipment, and facility expenses. Efficient manufacturing processes can help reduce overhead costs, allowing for competitive pricing.
-
Tooling: Although 3D printing minimizes the need for extensive tooling compared to traditional manufacturing, some processes may still require specific tools or molds. These costs should be factored into the pricing strategy.
-
Quality Control (QC): Ensuring the implants meet regulatory and safety standards incurs costs related to testing and certification. Buyers should seek suppliers with robust QC processes, as this can prevent costly recalls or legal issues down the line.
-
Logistics: Shipping and handling costs can vary greatly depending on the location of the supplier and the destination. International buyers should consider Incoterms (International Commercial Terms) that define responsibilities for shipping, duties, and insurance.
-
Margin: Supplier margins can vary, influenced by market demand and competition. Understanding the typical markups in your specific market can aid in negotiation.
Price Influencers
-
Volume/MOQ: Ordering in larger quantities often results in lower per-unit costs. Establishing a minimum order quantity (MOQ) with suppliers can help manage inventory and reduce costs.
-
Specifications/Customization: Custom implants tailored to specific patient needs may incur higher costs due to additional design and manufacturing processes. Buyers should weigh the benefits of customization against the cost implications.
-
Quality/Certifications: Implants that meet higher quality standards or possess relevant certifications (e.g., ISO, CE marking) typically command higher prices. Buyers should assess the importance of these certifications in their market context.
-
Supplier Factors: The reliability and reputation of suppliers can also affect pricing. Established suppliers with proven track records may charge a premium but offer greater assurance of quality and service.
Buyer Tips
-
Negotiation: Engage suppliers in discussions about pricing structures and potential discounts for bulk purchases. Be clear about your budget constraints while remaining open to compromise.
-
Cost Efficiency: Evaluate the Total Cost of Ownership (TCO), which includes not only the initial purchase price but also long-term costs associated with quality, durability, and maintenance.
-
Pricing Nuances: Be aware of regional pricing variations. For instance, suppliers in Europe may have different pricing strategies compared to those in Africa or South America due to economic conditions and competition levels.
-
Logistics Considerations: Factor in the total logistics costs when comparing suppliers, including shipping times and reliability. International buyers should also be mindful of potential customs delays or additional fees.
Disclaimer
Prices for 3D printed dental implants can vary significantly based on the factors mentioned above. It is advisable for buyers to obtain multiple quotes and perform thorough due diligence before making purchasing decisions.
Spotlight on Potential 3d printed dental implants Manufacturers and Suppliers
This section looks at several manufacturers active in the ‘3d printed dental implants’ market. This is a representative sample for illustrative purposes; B2B buyers must conduct extensive due diligence before any transaction. Information is synthesized from public sources and general industry knowledge.
Essential Technical Properties and Trade Terminology for 3d printed dental implants
Key Technical Properties of 3D Printed Dental Implants
Understanding the essential technical properties of 3D printed dental implants is crucial for B2B buyers to make informed purchasing decisions. Here are some critical specifications to consider:
-
Material Grade
– Definition: This refers to the specific type of material used in the production of dental implants, commonly titanium, zirconia, or specific polymers.
– B2B Importance: The choice of material affects the implant’s strength, biocompatibility, and longevity. Buyers must select materials that meet local regulatory standards and patient-specific needs. -
Dimensional Tolerance
– Definition: This specification indicates the allowable variation in the dimensions of the implants, typically measured in micrometers (µm).
– B2B Importance: High precision is critical in dental applications to ensure proper fit and functionality. Implants that do not meet dimensional tolerances may lead to complications, requiring costly adjustments or replacements. -
Surface Roughness
– Definition: This property describes the texture of the implant’s surface, which can influence osseointegration (the process of bone bonding to the implant).
– B2B Importance: A rougher surface can promote better bone integration, enhancing the implant’s stability. Buyers should assess surface treatment processes that optimize this property for specific applications. -
Porosity
– Definition: Porosity refers to the presence of microscopic pores within the implant material, which can influence its mechanical properties and biological performance.
– B2B Importance: Controlled porosity can enhance bone ingrowth and reduce the weight of the implant. It’s essential for buyers to understand the implications of porosity on the implant’s strength and integration with bone. -
Fatigue Strength
– Definition: This property measures the ability of the implant to withstand cyclic loading over time without failure.
– B2B Importance: High fatigue strength is vital for dental implants subjected to regular chewing forces. Buyers must ensure that the implants are tested for fatigue limits to avoid premature failures. -
Biocompatibility
– Definition: This property assesses how well the implant material interacts with biological tissues without causing adverse reactions.
– B2B Importance: Ensuring that implants are biocompatible is crucial for patient safety and regulatory compliance. Buyers should prioritize materials that have proven biocompatibility in clinical studies.
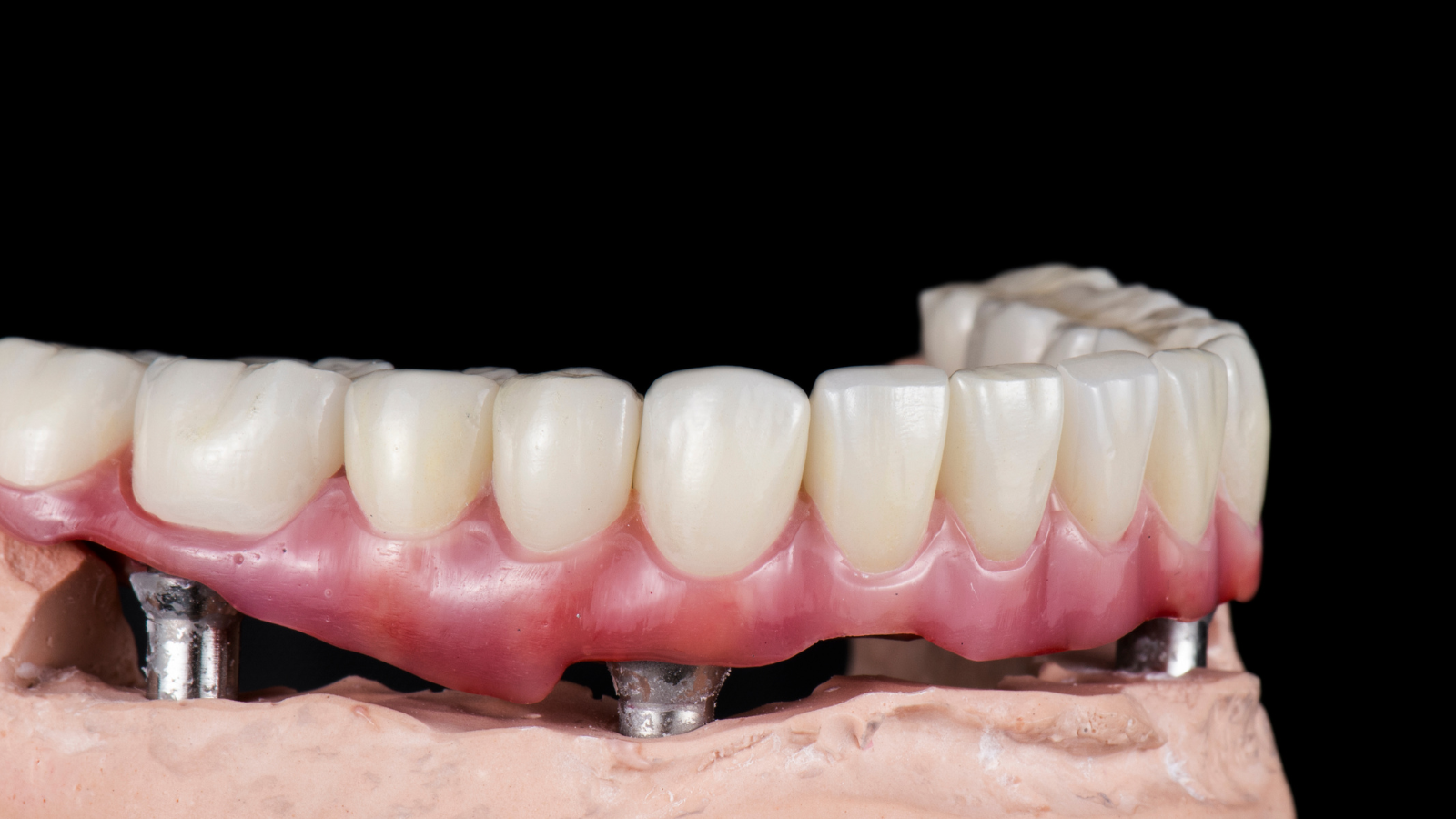
Illustrative Image (Source: Google Search)
Common Trade Terminology in Dental Implant Procurement
Familiarity with industry jargon can facilitate smoother transactions and negotiations. Here are several key terms to understand:
-
OEM (Original Equipment Manufacturer)
– Definition: A company that produces parts or equipment that may be marketed by another manufacturer.
– B2B Importance: Buyers often deal with OEMs for sourcing high-quality implants and components. Knowing the OEM can help in assessing product reliability. -
MOQ (Minimum Order Quantity)
– Definition: The smallest quantity of a product that a supplier is willing to sell.
– B2B Importance: Understanding MOQ helps buyers manage inventory costs and negotiate better pricing. Suppliers may have different MOQs based on the product type and production capabilities. -
RFQ (Request for Quotation)
– Definition: A document used to solicit price quotes from suppliers for specific products or services.
– B2B Importance: An RFQ is essential for comparing prices and terms from multiple suppliers, enabling buyers to make cost-effective purchasing decisions. -
Incoterms (International Commercial Terms)
– Definition: A set of international rules that define the responsibilities of sellers and buyers for the delivery of goods under sales contracts.
– B2B Importance: Understanding Incoterms can clarify shipping responsibilities, costs, and risks, which is vital for international transactions. -
Lead Time
– Definition: The amount of time from placing an order to receiving the goods.
– B2B Importance: Knowing the lead time helps buyers plan their inventory and ensure they meet patient needs without delay. -
Certification
– Definition: Official confirmation that a product meets specific standards or regulations, often required for medical devices.
– B2B Importance: Certifications ensure that products are safe and effective, which is crucial for compliance in different markets, particularly in healthcare.
By understanding these technical properties and trade terms, international B2B buyers can enhance their procurement strategies for 3D printed dental implants, ensuring they meet both quality standards and market demands.
Navigating Market Dynamics, Sourcing Trends, and Sustainability in the 3d printed dental implants Sector
Market Overview & Key Trends
The global market for 3D printed dental implants is undergoing transformative changes driven by technological advancements, increasing demand for personalized dental solutions, and rising awareness of the benefits of 3D printing. Key drivers include the growing prevalence of dental disorders, an aging population, and the demand for minimally invasive procedures. Notably, B2B buyers from Africa, South America, the Middle East, and Europe are increasingly seeking innovative solutions that can reduce costs and improve patient outcomes.
Emerging trends in sourcing and technology include the adoption of biocompatible materials such as titanium and zirconia, which are crucial for implant durability and patient safety. Additionally, the integration of digital workflows and software solutions that facilitate the design and production of custom implants is becoming more prevalent. This shift towards digital solutions allows for more accurate and efficient production, catering to the unique anatomical requirements of individual patients.
International buyers should also be aware of the global supply chain dynamics, which are influenced by geopolitical factors, trade agreements, and regional regulations. The increasing focus on local sourcing in regions like Africa and South America presents opportunities for partnerships with local manufacturers, enhancing supply chain resilience while reducing lead times and costs.
Sustainability & Ethical Sourcing in B2B
Sustainability is becoming a crucial factor in the procurement of 3D printed dental implants. The environmental impact of traditional manufacturing processes has prompted a shift towards more sustainable practices. For B2B buyers, prioritizing suppliers that utilize eco-friendly materials and energy-efficient production methods is essential. This can help mitigate the carbon footprint associated with dental implant production.
Moreover, ethical sourcing is gaining traction, with buyers increasingly interested in the supply chain practices of their suppliers. Ensuring that materials are sourced responsibly, without harming communities or ecosystems, is vital. Certifications such as ISO 14001 (Environmental Management) and adherence to ethical labor practices can serve as important indicators of a supplier’s commitment to sustainability.
Buyers should also consider the use of recyclable materials in the production of dental implants. This not only addresses environmental concerns but can also reduce costs in the long run. By fostering relationships with manufacturers who prioritize sustainability, B2B buyers can enhance their brand reputation and appeal to environmentally conscious consumers.
Brief Evolution/History
The evolution of 3D printed dental implants dates back to the early 2000s when the technology began to gain traction in the dental field. Initially limited to prototyping, advancements in additive manufacturing have enabled the production of fully functional implants. Early adopters focused on creating custom prosthetics, but as technology matured, the scope expanded to include a variety of dental applications.
Today, 3D printing is recognized for its ability to produce complex geometries and personalized solutions at a fraction of the time and cost compared to traditional methods. This evolution has not only improved patient outcomes but has also opened new markets for B2B buyers seeking innovative solutions in the dental sector. As the technology continues to advance, the potential for 3D printed dental implants will only increase, offering exciting opportunities for forward-thinking businesses.
Frequently Asked Questions (FAQs) for B2B Buyers of 3d printed dental implants
-
What should I consider when vetting suppliers of 3D printed dental implants?
When vetting suppliers, prioritize their certifications, such as ISO 13485 for medical devices, and verify their compliance with local regulations in your region. Assess their manufacturing capabilities, including technology used and production capacity. Request references or case studies from other clients, particularly those in similar markets. It’s also beneficial to conduct site visits or virtual audits to evaluate their quality control processes and overall operational standards. -
Can I customize 3D printed dental implants to meet specific patient needs?
Yes, many suppliers offer customization options for 3D printed dental implants. Discuss your specific requirements, such as implant size, shape, and material, with potential suppliers. Ensure they have the necessary technology and expertise to meet your customization needs. Request samples or prototypes to evaluate the quality and fit before placing a bulk order, as this can significantly impact patient outcomes. -
What are the minimum order quantities (MOQ) and lead times for 3D printed dental implants?
MOQs and lead times can vary widely among suppliers. Typically, smaller orders may have higher per-unit costs, while larger orders often benefit from economies of scale. Lead times can range from a few days to several weeks, depending on the complexity of the design and the supplier’s production capacity. It’s advisable to clarify these details upfront to align your procurement strategy with your business needs. -
What payment terms should I expect when sourcing 3D printed dental implants?
Payment terms can differ by supplier but commonly include options such as upfront payment, partial payments upon order confirmation, or net payment terms post-delivery. When negotiating, consider factors like order size and your relationship with the supplier. Always ensure that payment methods are secure, and consider using escrow services for larger transactions to mitigate financial risks.
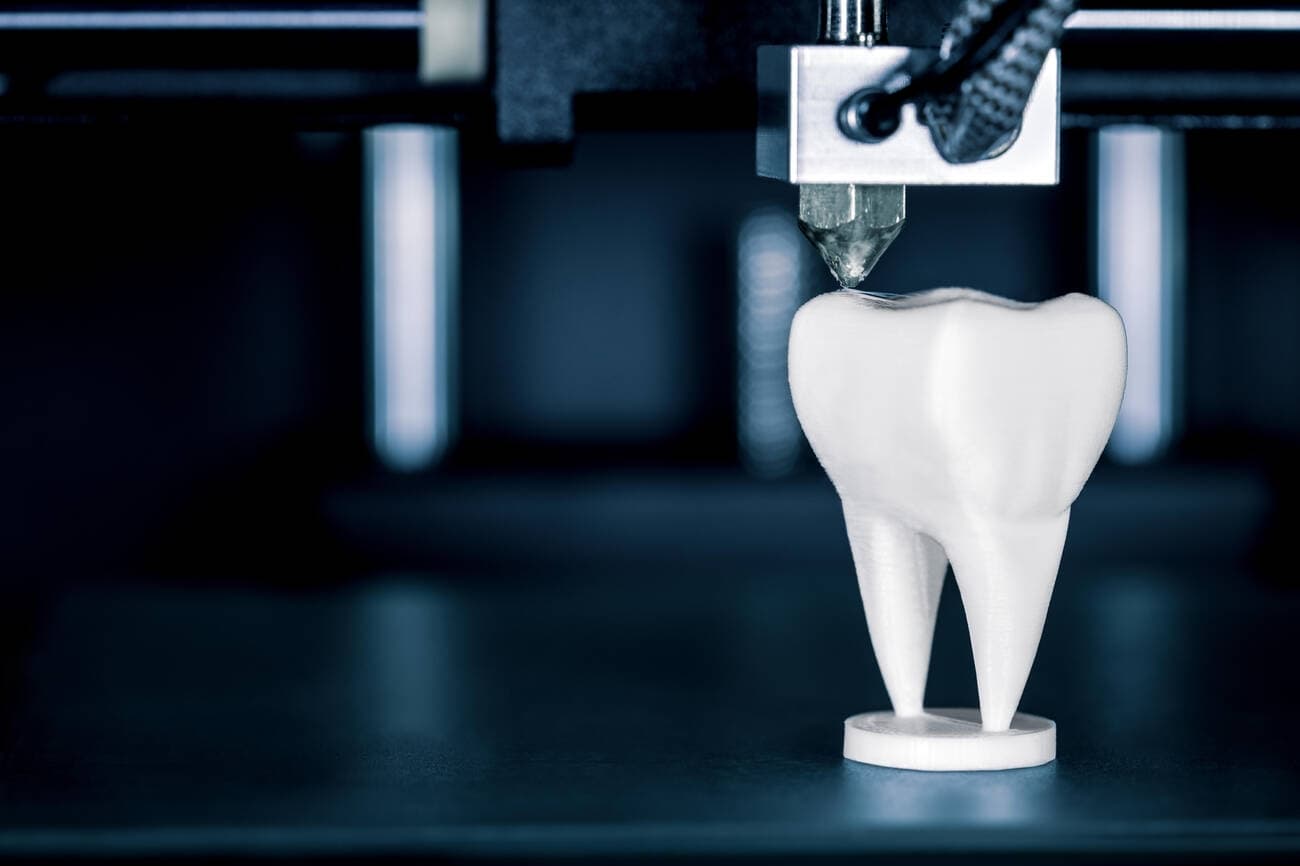
Illustrative Image (Source: Google Search)
-
How do I ensure quality assurance and certification for the implants I purchase?
To ensure quality, request documentation of certifications relevant to dental implants, such as CE marking in Europe or FDA approval in the U.S. Verify the supplier’s quality control processes, including their inspection and testing protocols. Additionally, consider third-party audits or inspections to confirm compliance with industry standards, and maintain a clear communication channel for addressing any quality concerns post-delivery. -
What logistical considerations should I keep in mind when importing dental implants?
Logistics play a critical role in the timely delivery of dental implants. Understand the import regulations specific to your country, including customs duties and tariffs. Choose reliable shipping methods that ensure the integrity of the implants during transit. Collaborate with logistics providers experienced in handling medical devices to manage potential delays or complications effectively, especially in cross-border shipments. -
How can I address disputes with suppliers over quality or delivery issues?
Establish clear communication and documentation practices from the outset to minimize disputes. Create a contract that includes terms for quality standards, delivery timelines, and remedies for non-compliance. If issues arise, address them promptly through direct communication with the supplier. If necessary, consider mediation or arbitration as a means of resolving disputes without resorting to litigation, which can be costly and time-consuming. -
What emerging trends should I watch for in the 3D printed dental implant market?
Stay informed about advancements in materials and printing technologies that enhance the performance and biocompatibility of dental implants. Innovations such as bioactive materials and integrated digital workflows are gaining traction. Additionally, keep an eye on regulatory changes that could affect the market landscape. Engaging with industry trade shows, webinars, and professional associations can provide valuable insights into emerging trends and best practices in the field.
Important Disclaimer & Terms of Use
⚠️ Important Disclaimer
The information provided in this guide, including content regarding manufacturers, technical specifications, and market analysis, is for informational and educational purposes only. It does not constitute professional procurement advice, financial advice, or legal advice.
While we have made every effort to ensure the accuracy and timeliness of the information, we are not responsible for any errors, omissions, or outdated information. Market conditions, company details, and technical standards are subject to change.
B2B buyers must conduct their own independent and thorough due diligence before making any purchasing decisions. This includes contacting suppliers directly, verifying certifications, requesting samples, and seeking professional consultation. The risk of relying on any information in this guide is borne solely by the reader.
Strategic Sourcing Conclusion and Outlook for 3d printed dental implants
In conclusion, the strategic sourcing of 3D printed dental implants represents a transformative opportunity for international B2B buyers, particularly in emerging markets across Africa, South America, the Middle East, and Europe. By leveraging the advantages of 3D printing—such as customization, reduced lead times, and enhanced biocompatibility—businesses can significantly improve patient outcomes and operational efficiencies.
Key Takeaways:
– Cost Efficiency: 3D printing reduces material waste and manufacturing costs, making high-quality dental solutions more accessible.
– Customization: Tailored solutions enhance patient satisfaction and can lead to improved clinical results.
– Supply Chain Flexibility: On-demand manufacturing capabilities can mitigate supply chain disruptions, particularly vital in today’s global market.
As the dental industry continues to evolve, investing in strategic sourcing practices will be crucial for maintaining a competitive edge. Now is the time for B2B buyers to explore partnerships with innovative suppliers who can deliver cutting-edge solutions in 3D printed dental implants. Embrace this technology to meet the growing demands of your clientele and position your business for future success.